In today’s competitive industrial landscape, companies are under increasing pressure to enhance productivity while minimizing their environmental footprint. One of the most effective ways to achieve this balance is through the use of energy-efficient equipment. For businesses that rely on caustic soda mixing processes, investing in energy-efficient caustic mixers can lead to significant cost savings and improved sustainability. In this article, we will explore how modern energy-saving technologies in caustic mixers are not only helping businesses reduce energy consumption but also optimizing operational performance. Whether you're a large-scale manufacturer or a small-scale operator, adopting these innovations can transform your operations and contribute to a more sustainable and profitable future.
Table of contents:
Variable Frequency Drive (VFD): Precision Control for Maximum Efficiency
High-Efficiency Motors and Low-Energy Drive Systems
Automatic Speed Regulation and Load Matching
Heat Recovery Systems: Reusing Energy for Greater Sustainability
Smart Monitoring and Optimization for Continuous Efficiency
Improved Equipment Longevity and Reduced Maintenance Costs
Enhanced Sustainability and Environmental Responsibility
Variable Frequency Drive (VFD): Precision Control for Maximum Efficiency
Variable Frequency Drive (VFD) technology has become a game-changer for many industrial applications, and caustic mixers are no exception. Traditionally, electric motors in mixing equipment would operate at a fixed speed, consuming a consistent amount of power regardless of the actual demand. This often led to unnecessary energy wastage, especially during periods of low workload.
With VFD, the motor speed is dynamically adjusted to match the exact needs of the caustic mixing process. When the load is low, the motor runs at a reduced speed, thereby consuming less energy. Conversely, when higher output is needed, the VFD increases the motor speed accordingly. This flexibility ensures that energy consumption is directly proportional to the task at hand, leading to substantial energy savings over time.
For industries where energy costs are a significant part of operational expenses, adopting caustic mixers with VFD technology can provide an immediate reduction in electricity consumption, lowering operating costs while improving efficiency.
High-Efficiency Motors and Low-Energy Drive Systems
The efficiency of a caustic mixer is heavily influenced by the type of motor it uses. High-efficiency motors (such as those with IE3 or higher ratings) are designed to maximize power output while minimizing energy loss. These motors consume less power compared to conventional models, allowing businesses to operate their caustic mixers with a reduced environmental impact.
In addition to high-efficiency motors, low-energy drive systems further enhance energy conservation. These systems intelligently adjust the power output based on the requirements of the caustic mixing process, ensuring that the equipment operates at peak efficiency across a wide range of conditions. By reducing energy consumption and improving motor performance, businesses can optimize both their energy bills and overall equipment lifespan.
Automatic Speed Regulation and Load Matching
One of the most innovative features of modern caustic mixers is their ability to automatically adjust mixing speed based on real-time workload demands. This is crucial for industries where the intensity of mixing may vary depending on the consistency or volume of materials involved.
Automatic speed regulation allows the caustic mixer to match its operational power to the workload, reducing excess energy consumption during periods of low mixing intensity. For example, when mixing smaller batches or lighter materials, the system automatically lowers its speed, consuming only the necessary amount of energy. On the other hand, when handling larger batches or more viscous materials, the system ramps up its power to ensure optimal mixing performance. This automatic adjustment prevents energy waste and helps companies avoid overexerting their equipment.
Heat Recovery Systems: Reusing Energy for Greater Sustainability
In many industrial operations, heat is a byproduct of mixing processes, including caustic soda mixing. Without an energy recovery system, this excess heat often goes to waste. However, with the implementation of heat recovery systems, businesses can capture and reuse the heat generated during the mixing process.
For instance, the excess heat produced by a caustic mixer can be redirected to preheat other chemicals or materials involved in the production process, reducing the need for external heating sources. This not only minimizes energy consumption but also enhances the overall energy efficiency of the entire production line.
Heat recovery systems, when combined with energy-efficient caustic mixers, create a closed-loop system that reduces overall energy expenditure. As a result, businesses can lower operational costs while promoting sustainability.
Smart Monitoring and Optimization for Continuous Efficiency
The integration of Internet of Things (IoT) technology and smart monitoring systems into caustic mixers enables real-time tracking of energy consumption and equipment performance. This constant flow of data helps operators make informed decisions on when to adjust parameters to maximize energy efficiency.
Smart monitoring systems provide insights into factors such as motor performance, load variations, and energy usage patterns. This data can be analyzed to detect inefficiencies or irregularities in the mixing process, allowing operators to optimize operations further. In addition, many modern caustic mixers offer remote access to these systems, enabling operators to adjust settings and troubleshoot issues even when they are not on-site.
By continuously optimizing the mixing process based on real-time data, businesses can maintain a high level of energy efficiency while ensuring that their caustic mixers are always operating at peak performance.
Improved Equipment Longevity and Reduced Maintenance Costs
Energy-efficient caustic mixers often require less maintenance compared to traditional models. By operating more efficiently, they experience less wear and tear, which can result in longer equipment lifespans. Furthermore, systems that are designed to minimize energy consumption tend to be more robust, reducing the frequency and cost of repairs.
With automatic speed regulation, VFD technology, and high-efficiency motors, these mixers require fewer interventions, enabling companies to maintain smooth operations with minimal downtime.
Enhanced Sustainability and Environmental Responsibility
In today's global market, sustainability is not just a buzzword—it's a business imperative. By investing in energy-efficient caustic mixers, companies demonstrate their commitment to environmental responsibility. The reduced energy consumption and lower carbon footprint of these mixers contribute to greener operations, which can enhance a company's reputation among environmentally-conscious customers and stakeholders.
Moreover, many governments offer incentives for businesses that adopt energy-efficient technologies, further improving the financial viability of upgrading to modern, eco-friendly caustic mixers.
Energy-efficient caustic mixers are transforming the way industries operate, offering significant savings on energy costs while also contributing to a more sustainable and eco-friendly production process. By incorporating advanced technologies such as Variable Frequency Drives, high-efficiency motors, automatic load matching, and heat recovery systems, businesses can reduce energy consumption, increase equipment longevity, and improve overall operational efficiency. For businesses looking to stay ahead of the competition while reducing their environmental footprint, investing in energy-efficient caustic mixers is a smart choice. To explore how these cutting-edge solutions can benefit your operations, visit PRM Drilling, a leading caustic mixer manufacturer.
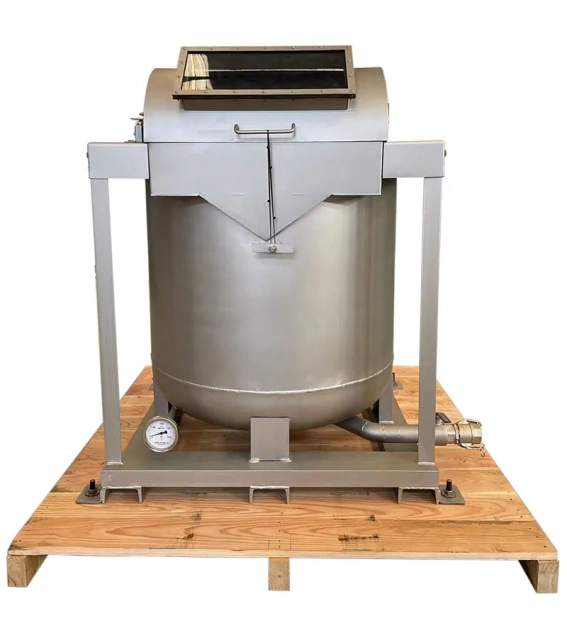