In today’s fast-paced world of technological advancement, the electronics industry drives progress but also contributes significantly to resource consumption and waste. From smartphones to data centers, the demand for electronic devices is relentless. Yet, behind sleek designs and powerful processors lies a supply chain with serious environmental impacts. As sustainability becomes a priority for consumers, regulators, and corporations, manufacturers face growing pressure to adopt greener practices. This shift goes beyond energy efficiency, focusing on the materials and processes used to create the devices powering our modern world. Often overlooked, the enclosures housing sensitive components play a key role in protecting hardware and influencing a product’s environmental footprint. Among available materials, custom aluminum extrusions and extruded aluminum profiles, especially for formats like 19-inch rack-mount cases, stand out for their performance, durability, and eco-friendliness. This article explores why choosing custom aluminum extrusions and extruded aluminum is more than an engineering decision—it’s a step toward a more sustainable electronics industry.
Table of contents:
The Foundation: Aluminum's Inherent Sustainability Credentials
The Process Advantage: How Extrusion Enhances Sustainability
Durability by Design: Extending Lifespans, Reducing Waste
Beyond the Material and Design: The Role of Green Manufacturing Practices
Applications Driving the Green Transition: Where Sustainability Meets Performance
The Foundation: Aluminum's Inherent Sustainability Credentials
Aluminum's journey to becoming a cornerstone material for sustainable design is rooted in its fundamental properties. Unlike many materials that degrade significantly upon recycling, aluminum is infinitely recyclable without loss of quality. This characteristic is paramount in building a circular economy where resources are kept in use for as long as possible, extracting maximum value and then recovering and regenerating products and materials at the end of their service life.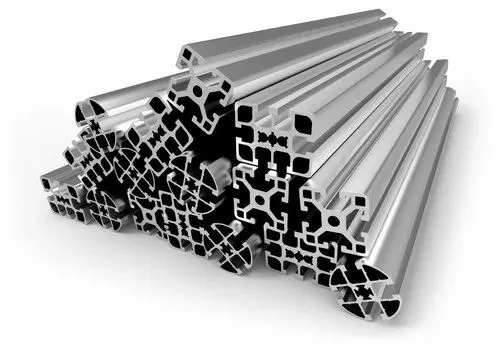
Energy Savings That Compound: The environmental benefits of recycling aluminum are staggering, primarily concerning energy consumption. Producing recycled aluminum requires only about 5% of the energy needed to create primary aluminum from raw bauxite ore. This drastic 95% energy saving translates directly into reduced greenhouse gas emissions, lower reliance on fossil fuels, and decreased environmental disruption associated with mining and refining virgin materials. Every time aluminum is recycled, these energy savings are realized again, creating a compounding positive impact over multiple product lifecycles.
Reducing the Mining Footprint: Bauxite mining, the source of primary aluminum, can have significant environmental consequences, including habitat destruction and water resource impacts. By prioritizing recycled aluminum content in extruded profiles, manufacturers directly reduce the demand for virgin ore, mitigating these upstream environmental pressures.
The Process Advantage: How Extrusion Enhances Sustainability
While the material itself is crucial, the manufacturing process used to shape it also significantly influences the overall environmental impact. Aluminum extrusion is a highly efficient process that offers unique advantages for creating sustainable electronic enclosures.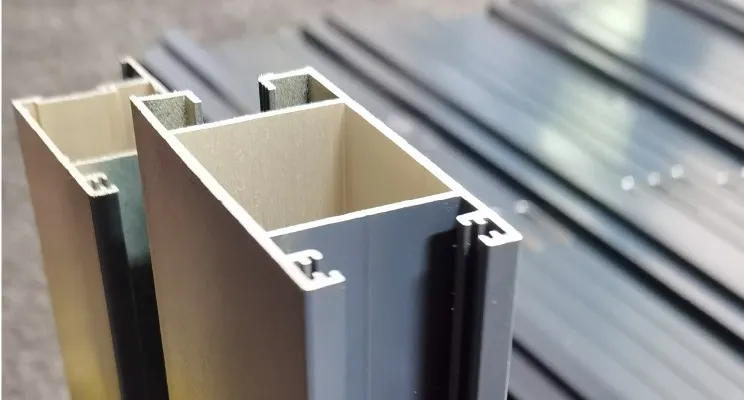
Design Integration and Complexity: Extrusion allows for the creation of intricate and highly functional profiles in a single piece. Features like heat sink fins, mounting channels, screw bosses, and snap-fit mechanisms can often be integrated directly into the extrusion design. This eliminates the need for multiple separate components, reducing the overall part count, assembly time, and potential points of failure. Fewer parts mean less material used overall and simplified end-of-life disassembly for recycling.
Customization for Optimization: The ability to create custom aluminum extrusions is a key sustainability enabler. Designers are not limited to standard off-the-shelf shapes. They can tailor the profile precisely to the application's needs, optimizing structural support, thermal management, and spatial efficiency. This bespoke approach ensures that no excess material is used purely due to design constraints imposed by standard shapes. Efficient design directly translates to resource conservation.
Therefore, the extrusion process complements aluminum's inherent recyclability by enabling the creation of optimized, resource-efficient, and highly functional components like the profiles used in 19-inch cases.
Durability by Design: Extending Lifespans, Reducing Waste
One of the most effective ways to reduce the environmental impact of any product is to extend its usable lifespan. Frequent replacement cycles consume more resources, generate more manufacturing emissions, and create more end-of-life waste. Extruded aluminum profiles for 19-inch cases excel in providing the durability needed for long service life in demanding electronic applications.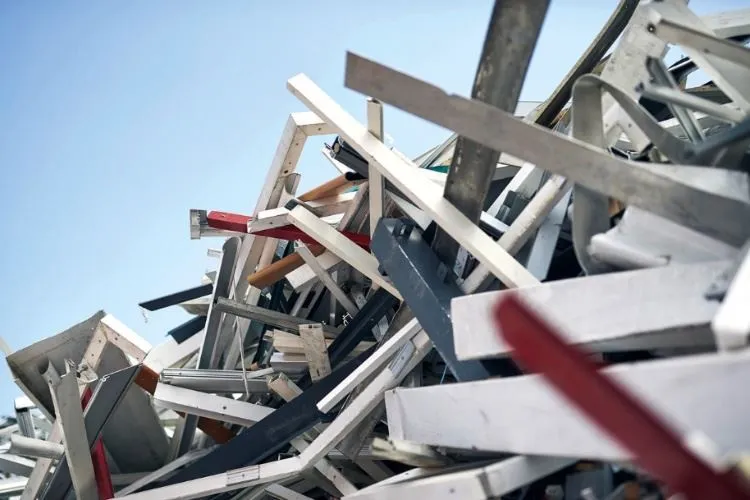
Exceptional Strength-to-Weight Ratio: Aluminum offers impressive structural rigidity relative to its weight. Extruded profiles can be designed to provide robust support and protection for sensitive electronic components housed within the 19-inch case. This strength ensures the enclosure can withstand physical stresses during transport, installation, and operation, reducing the risk of damage that could lead to costly repairs or disposal. The lightweight nature also contributes to lower transportation emissions.
Integrated Thermal Management: Effective heat dissipation is essential for the reliability and lifespan of electronic components. Overheating is a major cause of device failure, leading to shorter lifespans and more e-waste. The extrusion process enables seamless integration of heat sink fins into case profiles, creating an efficient passive cooling system that transfers heat away from critical components. This removes the need for additional, failure-prone cooling elements like fans (though fans can still be used). By keeping temperatures optimal, these thermal management features extend device lifespan and help reduce waste.
By designing for durability, manufacturers using extruded aluminum profiles effectively minimize the frequency of replacement, conserving resources and reducing the waste stream associated with discarded electronics.
Beyond the Material and Design: The Role of Green Manufacturing Practices
True sustainability encompasses the entire manufacturing ecosystem. Choosing an eco-friendly material like aluminum and an efficient process like extrusion is essential, but responsible manufacturers go further by implementing green practices throughout their operations.
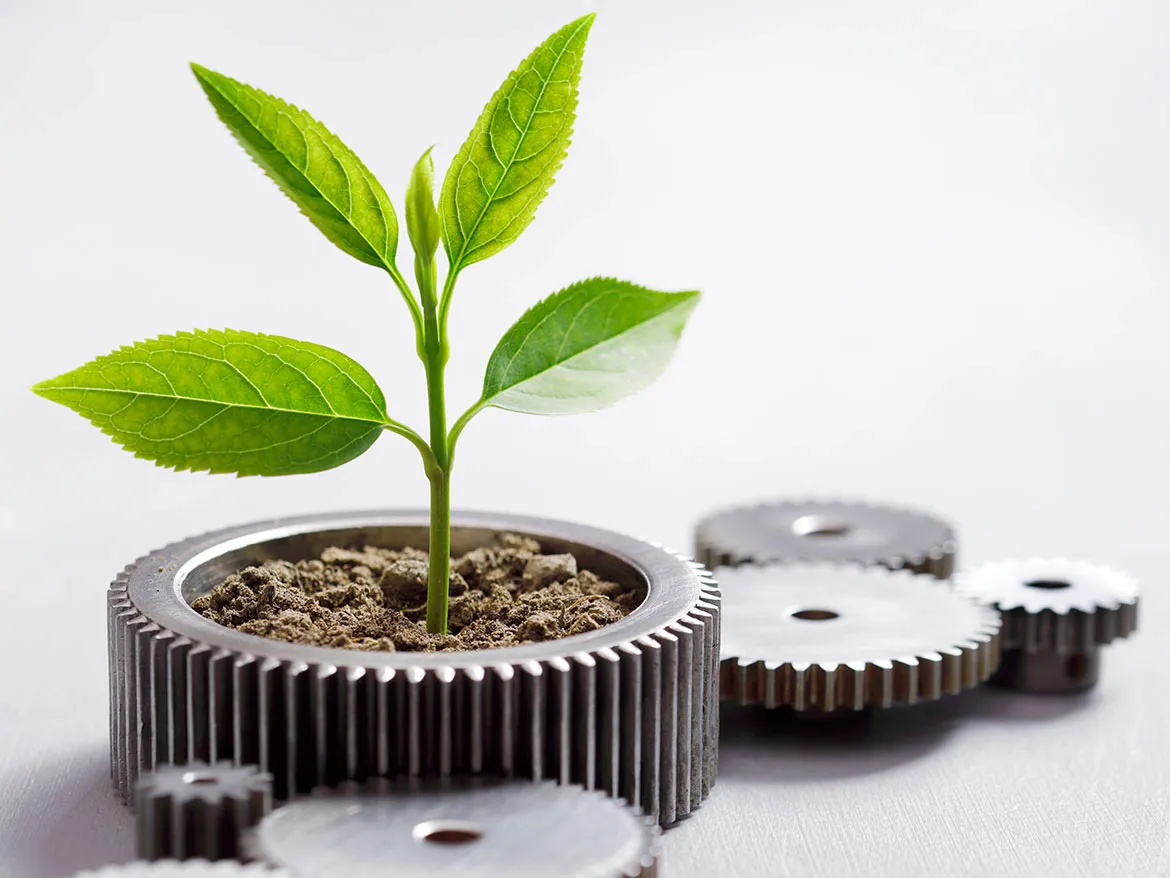
Energy Efficiency in Production: Leading extrusion facilities invest in modern, energy-efficient presses, heaters, and handling equipment. Optimizing heating cycles, utilizing regenerative braking systems, and implementing smart energy management protocols can significantly reduce the energy consumed per unit of extruded profile, lowering the carbon footprint of the manufacturing stage. Some facilities are also exploring or implementing the use of renewable energy sources to power their operations.
Waste Minimization and Resource Optimization: Beyond the inherent material efficiency of extrusion, conscious manufacturers implement rigorous scrap management programs. This involves careful segregation of different aluminum alloys, efficient collection of offcuts and end pieces, and closed-loop systems where scrap is directly remelted and reused internally or sent to specialized recyclers. Water usage in cooling and finishing processes is also monitored and minimized.
Compliance and Chemical Safety: Compliance with environmental regulations like RoHS and REACH is essential for sustainable manufacturing. These standards limit harmful materials in electronics, making products safer and easier to recycle or dispose of responsibly. Working with compliant suppliers ensures components improve the product’s environmental impact.
When sourcing components like 19-inch case profiles, it's crucial to partner with custom aluminum extrusions suppliers who not only offer high-quality products but also demonstrate a clear commitment to these green manufacturing principles. Their practices directly impact the embodied energy and overall sustainability of the final electronic product.
Applications Driving the Green Transition: Where Sustainability Meets Performance
The benefits of using sustainable extruded aluminum 19-inch cases are being realized across a growing range of industries, particularly those inherently focused on environmental responsibility or requiring high reliability.Renewable Energy Systems: Solar inverters, wind turbine controllers, and energy storage management systems often rely on robust 19-inch rack enclosures. The durability, corrosion resistance, and thermal management capabilities of extruded aluminum are ideal for these applications, which are frequently deployed in outdoor or demanding environments and are central to the clean energy transition.
Data Centers and IT Infrastructure: While data centers consume significant energy, there's a strong push for efficiency and sustainability (Green IT). Extruded aluminum rack-mount cases contribute by offering excellent thermal performance (reducing cooling energy needs), durability (long service life), and high recyclability at the end of the equipment lifecycle. Custom designs allow for optimized airflow and component density.
Industrial Automation and Control: Factory floors and process control environments often involve harsh conditions. Extruded aluminum enclosures provide the necessary protection and heat dissipation for sensitive control electronics, ensuring reliable operation and minimizing downtime and replacement cycles in industries striving for greater operational efficiency and reduced environmental impact.
Telecommunications: Base stations and network equipment frequently utilize 19-inch formats. The lightweight yet strong nature of aluminum extrusions is beneficial for installations, while their durability ensures long-term performance in various climates.
In these and other sectors, specifying extruded aluminum profiles is becoming a hallmark of quality and a tangible demonstration of a commitment to building more sustainable technological solutions.
The electronics industry is at a turning point. Reducing environmental impact is no longer optional—it’s a key part of responsible business. Materials and manufacturing choices, such as for 19-inch electronic cases, offer a chance to drive positive change.Extruded aluminum profiles stand out for their performance, durability, and sustainability. Aluminum’s recyclability and energy-saving reuse make it a smart choice.
The extrusion process further enhances this by enabling efficient, integrated designs through custom aluminum extrusions, optimizing function while minimizing waste. Its durability—corrosion resistance, strength, and thermal management—also extends product lifespans, helping tackle electronic waste.When combined with responsible manufacturing—energy efficiency, waste reduction, and compliance—these components support a greener electronics industry.
Partnering with knowledgeable custom aluminum extrusions suppliers who prioritize eco-friendly practices is key. Companies like Renxin play a crucial role in enabling the industry to create longer-lasting, more efficient, and sustainable electronic systems for the future.