In high-stakes environments like firefighting and emergency rescue, personal protective equipment isn't just gear; it's a lifeline. Head protection, specifically, stands as a critical barrier against immediate, life-threatening hazards. Traditionally, the focus in procurement has heavily leaned towards initial cost and immediate compliance. However, a more strategic and increasingly vital perspective is emerging – one that considers the entire lifecycle of the equipment. Extending the operational life of safety helmets, particularly those used in demanding rescue scenarios, offers a powerful combination of enhanced safety, significant long-term cost savings, and crucial environmental benefits. Safety products wholesale providers play a key role in this approach by offering durable and high-quality equipment designed for longevity. Reducing the frequency of replacement directly translates to conserving valuable resources and minimizing waste, aligning operational needs with growing corporate social responsibility mandates. This exploration delves into the key factors that contribute to helmet longevity and why prioritizing durability isn't just good practice, it's smart business and responsible stewardship.
Table of contents:
The Foundation: Material Durability as the First Line of Longevity
Built to Endure: The Critical Role of Structural Strength Design
Smart Sustainability: The Power of Replaceable Components and Modularity
Performance That Lasts: Ensuring Consistent Protection Over Time
One Helmet, Many Missions: Versatility Reduces Resource Consumption
Designed for Duty: The Importance of Easy Maintenance and Cleaning
The Bigger Picture: Environmental Significance and Total Cost of Ownership
The Foundation: Material Durability as the First Line of Longevity
The journey to a longer-lasting helmet begins with its very composition. Advanced materials science plays a pivotal role in defining how well a helmet withstands the rigors of its intended use. High-performance thermoplastics, such as Acrylonitrile Butadiene Styrene (ABS), are frequently specified for high-intensity rescue helmet shells. ABS offers an exceptional balance of properties: it boasts high tensile strength and rigidity, providing robust resistance against impacts from falling debris or collisions. Critically, it maintains its structural integrity across a range of temperatures, resisting the brittleness that can plague lesser materials in cold conditions and the softening that can occur under extreme heat, common in firefighting scenarios.
Beyond impact resistance, the materials used in a helmet play a key role in its durability against environmental and chemical challenges. Rescue operations expose equipment to intense UV radiation, high humidity, water, and chemicals like oils and fuels. Helmets made from materials resistant to chemical corrosion and UV damage last longer, avoiding fading, cracking, or polymer breakdown that can weaken both their look and protection. Abrasion resistance is also essential. Regular handling, surface contact, and storage can wear down inferior shells, potentially compromising protective layers. Durable materials ensure the helmet remains strong and presentable through repeated use, delaying replacement due to surface wear.
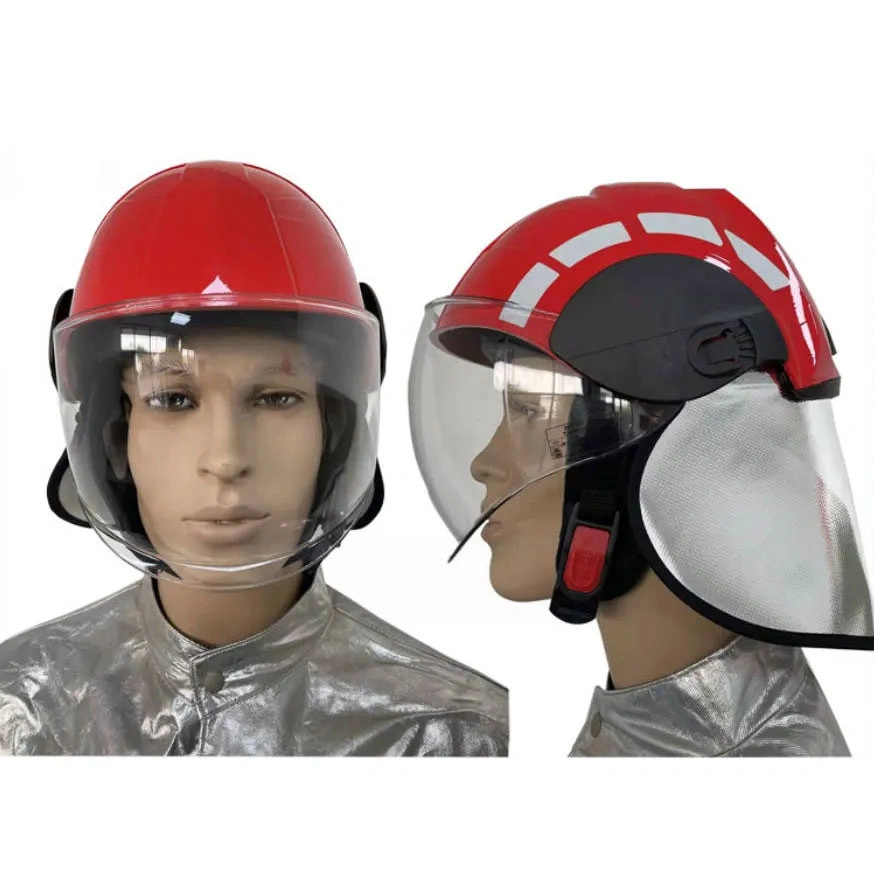
Built to Endure: The Critical Role of Structural Strength Design
While material choice provides the building blocks, the architectural design of the helmet is equally vital for longevity. How forces are distributed upon impact, how the components integrate, and the overall structural rigidity determine how well the helmet resists damage and wear over its lifetime. Modern rescue helmets often employ sophisticated internal suspension systems, such as multi-point harnesses (like six-point systems). These designs do more than just enhance comfort and fit; they distribute the force of an impact across a wider area of the shell and the wearer's head. This significantly reduces stress concentration on any single point, minimizing the risk of localized damage or cracking that could necessitate premature replacement.
The integration between the outer shell and the inner liner (often EPS foam for shock absorption) is another critical design consideration. A seamless, robust bond between these layers prevents delamination or separation, issues that can arise from repeated impacts, temperature fluctuations, or simply the aging of adhesives. An integrated structure maintains the helmet's overall stability and protective capability for longer. Furthermore, design elements focusing on inherent resistance to deformation are key. Helmets designed to withstand crushing forces or significant impacts without permanently warping or cracking are fundamentally more durable. They are less likely to be rendered unusable by the kind of incidental drops, bumps, or compressive forces that occur frequently in active rescue environments. This inherent toughness directly translates into a longer service life, reducing the frequency of replacements triggered by accidental damage.
Smart Sustainability: The Power of Replaceable Components and Modularity
A significant factor contributing to the premature disposal of safety equipment is the failure of a single, often minor, component. A traditional helmet design might necessitate discarding the entire unit if a chin strap frays, a sweatband wears out, or a visor gets scratched. This is where modularity offers a powerful advantage for extending product lifespan and reducing waste. Helmets designed with easily replaceable components shift the paradigm from wholesale replacement to targeted repair and refurbishment.
CComponents like chin straps, suspension harnesses, sweatbands, nape straps, and visors or goggles endure the most wear due to contact with the user and exposure to sweat, dirt, and stress. Designing these parts as modular and user-replaceable allows quick, cost-effective swaps when needed, restoring the helmet without discarding the durable shell. This reduces waste significantly, as only small, worn-out parts are replaced instead of the entire helmet. It also lowers the environmental impact by minimizing disposal and resource use. Additionally, replaceable visors and accessories enable customization, like adding or swapping helmet shields for specific needs or branding, without needing a new helmet. The economic benefits are clear—replacement parts cost far less than a new helmet, saving money in the long run.
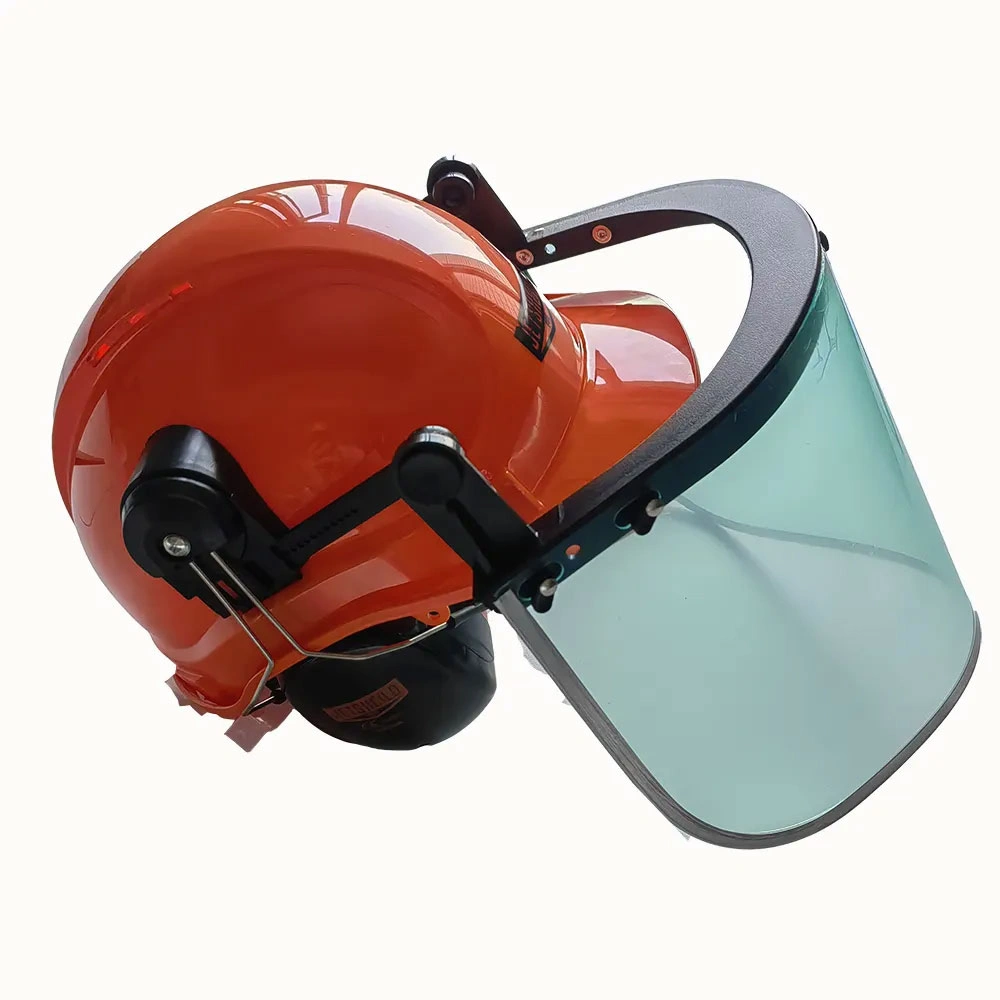
Performance That Lasts: Ensuring Consistent Protection Over Time
Safety certifications, such as EN 397 (Industrial Safety Helmets) or specific firefighting standards like EN 443, are crucial indicators of a helmet's initial protective capabilities. However, true longevity demands that these protective qualities remain stable throughout the helmet's intended service life. Helmets built with high-quality materials and robust construction are less susceptible to degradation that could compromise their performance over time. Certifications signify that the helmet met rigorous testing standards for impact absorption, penetration resistance, flame resistance (where applicable), and electrical insulation at the point of manufacture.
A well-engineered helmet maintains these properties even after prolonged exposure to operational stresses and environmental factors. The materials resist degradation from UV light, temperature cycles, and minor impacts, ensuring the shell doesn't become brittle or lose its shock-absorbing capacity prematurely. The integrity of the suspension system remains reliable, ensuring consistent fit and impact distribution. This sustained performance is critical not only for user safety but also for longevity. Helmets that rapidly degrade in protective capability, even if they appear physically intact, must be retired early. By investing in helmets designed for performance stability, organizations reduce the risk of needing to replace equipment simply because its certified protection level can no longer be guaranteed due to age or wear. This ensures continuous compliance and user safety while simultaneously extending the viable lifespan of the asset.
One Helmet, Many Missions: Versatility Reduces Resource Consumption
Specialization can lead to inefficiency and higher resource use. Requiring different helmet models for similar tasks increases inventory, complicates procurement, and results in more equipment being produced and discarded. Versatile, high-quality rescue helmets offer a more sustainable solution. A well-designed helmet certified for multiple environments—such as firefighting, technical rescue, construction, or industrial safety—can meet the needs of diverse teams or roles within an organization.
This multi-use capability simplifies procurement and inventory management. Instead of stocking separate helmets for different scenarios, organizations can standardize on one durable model, reducing the total number of helmets needed and cutting waste. For groups like municipal fire departments or industrial facilities with varied safety needs, a versatile helmet also simplifies training, maintenance, and logistics. This efficiency conserves resources, making versatility a critical part of sustainable equipment strategies.
Designed for Duty: The Importance of Easy Maintenance and Cleaning
The ease with which a helmet can be cleaned and maintained directly impacts its usability and lifespan. Helmets used in rescue environments inevitably get dirty, exposed to soot, grime, bodily fluids, oils, and other contaminants. Equipment that is difficult to clean may be neglected, leading to material degradation, unpleasant user experiences, or even potential health hazards. Worse, if cleaning procedures are too harsh or complex, they might inadvertently damage the helmet materials over time.
Helmets designed with smooth, non-porous outer shells made of materials resistant to common chemicals and grime are significantly easier to maintain. Surfaces that readily shed dirt and can be wiped clean with simple, approved cleaning agents ensure that decontamination protocols can be followed effectively without damaging the helmet. Features like removable and washable internal components (sweatbands, liners) further enhance hygiene and user comfort, prolonging the desirability of using the helmet. Simple, manufacturer-recommended maintenance procedures – such as periodic inspection of straps and buckles, checking the integrity of the shell, and proper cleaning – are easier to adhere to when the helmet's design facilitates them. This proactive care prevents minor issues from escalating and helps ensure the helmet reaches its maximum potential service life, reducing the likelihood of it being discarded prematurely due to poor condition or hygiene concerns.
The Bigger Picture: Environmental Significance and Total Cost of Ownership
Choosing durable, long-lasting rescue helmets goes beyond operational benefits—it reflects a commitment to sustainability and cost efficiency. Every time a helmet's replacement is delayed, the environmental impact of producing a new one is avoided. This includes the energy and resources used in material extraction, production, and transportation, all of which contribute to carbon emissions and resource depletion. Fewer replacements mean less consumption of plastics, metals, and energy, reducing the ecological footprint of an organization's safety program.
Extending product life also lowers the Total Cost of Ownership (TCO). While durable helmets may have a higher upfront cost, the savings from fewer replacements, reduced waste disposal, and streamlined inventory often result in a lower TCO over time. For organizations buying in bulk, these savings add up significantly. Investing in quality and durability means fewer helmets in landfills, reducing waste and plastic pollution while aligning with sustainability goals.
The decision to prioritize longevity in safety helmet procurement is a strategic one with far-reaching benefits. By focusing on durable materials, robust structural design, modularity for repairs, sustained protective performance, versatility across applications, and ease of maintenance, organizations can significantly extend the service life of this critical piece of PPE. This approach not only ensures unwavering protection for personnel operating in hazardous environments but also delivers considerable long-term cost savings and demonstrably reduces environmental impact through resource conservation and waste minimization. As organizations increasingly seek sustainable operational practices, choosing equipment designed for endurance is paramount. Companies prioritizing these long-term value propositions often look towards safety products manufacturers known for robust design and material science, such as the engineering seen in helmets from brands like HBC Safety, whose Ranger series exemplifies many of these durability, modularity, and multi-environment principles crucial for extending product life. Ultimately, investing in durable, long-lasting rescue helmets is an investment in the safety of people, the health of the planet, and the efficiency of the operation.