Ensuring the stability and efficiency of high-voltage power systems is paramount. Uncontrolled voltage fluctuations, particularly capacitive effects on long transmission lines or during light load conditions, can lead to equipment damage, operational inefficiencies, and even system instability. Shunt reactors, designed and supplied by leading manufacturers like Reactor Manufacturer, are indispensable components that counteract these issues by absorbing reactive power and stabilizing voltage levels. However, selecting the appropriate shunt reactor is a critical task demanding careful consideration of various technical and operational factors. Making the wrong choice can negate the intended benefits and potentially introduce new problems. This guide provides a systematic approach to help engineers, procurement managers, and project leads navigate the complexities of shunt reactor selection, ensuring optimal performance and reliability for their specific high-voltage applications.
Table of contents:
Defining the Operational Environment: Matching Application Scenario to Reactor Design
Sizing the Solution: Specifying Voltage Level and System Capacity
Clarifying the Functional Objective: Selecting the Right Reactor Type
Choosing the Construction: Dry-Type vs. Oil-Immersed Reactors
Verifying Quality and Compliance: Adherence to Industry Standards
Evaluating Supplier Capabilities: Beyond the Product Specifications
Defining the Operational Environment: Matching Application Scenario to Reactor Design
The first step in selecting a shunt reactor is a thorough understanding of where and how it will be deployed. The operational environment significantly influences the required design, materials, and protective features.
1.1. Identifying the Installation Location
- Substation Integration:Reactors installed within substations often need to integrate seamlessly with existing switchgear and control systems. Space constraints and connection points are primary considerations.
- Industrial Grid Support:Industrial facilities with large inductive loads or internal generation might require shunt reactors to manage voltage profiles and improve power factor locally. Proximity to sensitive processes may dictate specific noise or environmental requirements.
- Renewable Energy Interconnection:Wind and solar farms, often located remotely and connected via long cables, frequently experience capacitive effects. Shunt reactors are crucial for grid code compliance and stable power injection. The specific demands of intermittent generation must be factored in.
1.2. Assessing Environmental Conditions
- Indoor vs. Outdoor Deployment:This is a fundamental decision point. Indoor installations might prioritize lower noise levels and potentially smaller footprints, while outdoor units must withstand varying weather conditions, UV radiation, and potential pollution.
- Critical Environmental Factors:
- Altitude:Higher altitudes impact air density, affecting cooling efficiency and insulation requirements (dielectric strength). Derating factors may need to be applied.
- Temperature:Extreme ambient temperatures (both high and low) influence the reactor's thermal performance and material selection. Cooling systems must be designed for the maximum expected operating temperature.
- Humidity and Precipitation:High humidity, rain, snow, or ice accumulation necessitate appropriate enclosure protection (IP ratings) and robust insulation systems, particularly for outdoor units.
- Pollution and Dust:Industrial environments or coastal areas may expose the reactor to corrosive elements or conductive dust, requiring specific surface treatments, creepage distances, or sealed designs.
Understanding these application-specific nuances is crucial for guiding subsequent choices regarding reactor type, construction, and features.
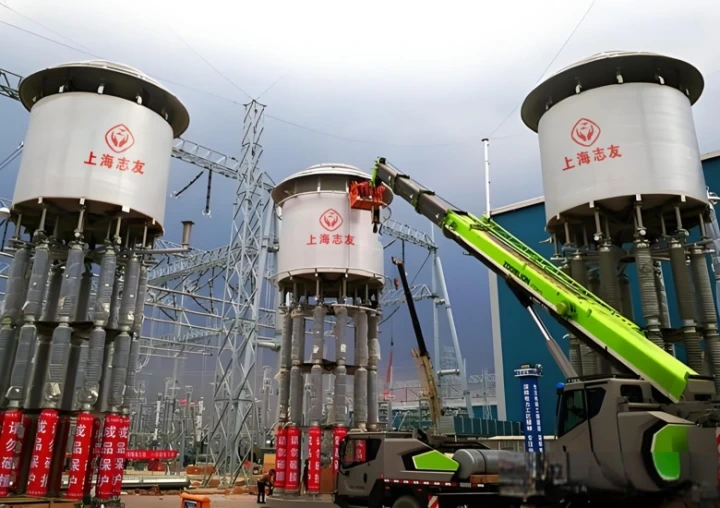
Sizing the Solution: Specifying Voltage Level and System Capacity
Once the application context is clear, the next critical step involves matching the shunt reactor's electrical characteristics to the power system's requirements.
2.1. Determining the Rated Voltage
- System Nominal Voltage:The reactor's rated voltage must correspond directly to the nominal voltage of the system segment where it will be connected. Common voltage levels include 10kV, 35kV, 66kV, 110kV, and higher transmission voltages. Selecting a reactor with an incorrect voltage rating can lead to insulation failure or inadequate performance.
- Insulation Level (BIL):Basic Insulation Level (BIL) requirements must also be considered, especially in systems prone to lightning strikes or switching surges. The reactor must withstand transient overvoltages typical for its voltage class.
2.2. Calculating Required Reactive Power Compensation
- System Analysis:Determining the exact amount of reactive power (measured in MVAr or kVAr) that needs compensation requires network studies. This analysis considers line length, cable capacitance, load profiles, and voltage regulation targets.
- Capacity Rating:The reactor's capacity rating defines how much reactive power it can absorb. It must be sufficient to counteract the system's excess capacitive reactive power under the intended operating conditions (e.g., light load).
2.3. Evaluating Current Handling Capabilities
- Continuous Current:The reactor must be designed to handle the continuous current associated with its rated voltage and reactive power.
- Short-Circuit Withstand:Equally important is the reactor's ability to withstand the mechanical and thermal stresses caused by system fault currents passing through it, even if only for a short duration. This ensures the reactor doesn't fail catastrophically during system disturbances. Manufacturers often specify short-time current ratings.
Clarifying the Functional Objective: Selecting the Right Reactor Type
Shunt reactors serve multiple purposes within a power system. Identifying the primary functional goal is key to selecting the most effective and economical type of reactor.
3.1. Voltage Control and Reactive Power Compensation
- Primary Function:This is the most common application. Shunt reactors are connected in parallel with the line to absorb surplus capacitive reactive power, thereby preventing voltage rise on long transmission lines or lightly loaded cables.
- Product Type:Standard Parallel Shunt Reactors are designed specifically for this purpose. Their inductance is optimized for efficient reactive power absorption at the system frequency.
3.2. Harmonic Filtering
- Primary Function:In systems with significant non-linear loads (like variable speed drives, rectifiers, or arc furnaces), harmonic currents can distort the voltage waveform. Filter reactors are used in conjunction with capacitor banks to create resonant circuits tuned to specific harmonic frequencies, effectively trapping and removing them from the system.
- Product Type:Filter Reactors (Tuned or Detuned) are required. These reactors are designed not only for their fundamental frequency inductance but also to handle harmonic currents and potentially higher thermal stresses. They form part of a larger harmonic filter bank.
3.3. Fault Current Limiting
- Primary Function:In some network configurations, particularly near generation sources or where system impedance is low, prospective fault currents can exceed the rating of downstream equipment (like circuit breakers). Series or special types of shunt reactors can be used to introduce additional impedance during fault conditions, limiting the fault current magnitude.
- Product Type:Fault Current Limiting Reactors (series type is more common, but specialized shunt configurations exist) are specifically designed for high short-circuit withstand capabilities and optimized impedance characteristics under fault conditions.
3.4. Other Specialized Applications
- Neutral Grounding:Neutral Grounding Reactors are used to limit ground fault currents in solidly grounded or impedance-grounded systems.
- Thyristor Controlled Reactors (TCR):Used in Static Var Compensators (SVCs) for dynamic and rapid control of reactive power.
Clearly defining whether the main goal is steady-state voltage control, harmonic mitigation, or fault protection ensures the selection of a reactor optimized for that task.
Choosing the Construction: Dry-Type vs. Oil-Immersed Reactors
The physical construction of the shunt reactor profoundly impacts its installation requirements, maintenance needs, safety profile, and suitability for different environments.
4.1. Dry-Type Air Core Reactors
- Construction:Windings are typically made of copper or aluminum conductors, insulated and supported by non-metallic structures, and cooled by natural or forced air. They contain no oil.
- Advantages:
- Safety:No risk of oil leaks or fire, making them ideal for indoor installations, urban areas, or environmentally sensitive locations.
- Environmental Friendliness:No oil disposal concerns.
- Maintenance:Generally lower maintenance requirements (no oil testing or filtration).
- Considerations:
- Typically larger footprint for equivalent ratings compared to oil-immersed.
- More susceptible to airborne contaminants if not properly enclosed.
- Cooling efficiency can be affected by ambient temperature and altitude.
4.2. Oil-Immersed Reactors
- Construction:Core and windings are immersed in insulating mineral oil within a sealed tank. Cooling often involves radiators and sometimes fans or pumps (ONAN, ONAF, OFAF).
- Advantages:
- Compactness:Higher power density allows for smaller size for a given rating.
- Insulation:Oil provides excellent dielectric strength and cooling.
- Environmental Protection:Sealed tank offers good protection against harsh environments. Ideal for outdoor, high-voltage, and high-power applications.
- Considerations:
- Fire Risk:Oil is flammable, requiring specific safety measures (fire walls, containment pits).
- Environmental Risk:Potential for oil leaks requires monitoring and containment provisions.
- Maintenance:Requires periodic oil sampling and testing; potential for oil filtration or replacement.
The choice between dry-type and oil-immersed often hinges on installation location, safety regulations, environmental policies, and total cost of ownership including maintenance.
Verifying Quality and Compliance: Adherence to Industry Standards
Reliability and safety are non-negotiable in high-voltage systems. Ensuring the shunt reactor meets recognized industry standards is crucial for guaranteeing performance and interoperability.
5.1. International and Regional Standards
- Key Standards:Look for compliance with major international standards like IEC (International Electrotechnical Commission), ANSI/IEEE (American National Standards Institute/Institute of Electrical and Electronics Engineers), or relevant regional/national standards (e.g., GB standards in China). Compliance ensures the reactor meets globally accepted benchmarks for design, performance, and safety.
- Verification:Reputable manufacturers provide documentation and type test reports certifying compliance.
5.2. Essential Type Tests and Quality Checks
- Insulation Level Tests:Verifies the reactor's ability to withstand rated voltage and transient overvoltages (lightning impulse, switching impulse).
- Temperature Rise Test:Ensures the reactor operates within safe temperature limits under continuous load, preventing premature degradation of insulation.
- Short-Circuit Withstand Test:Confirms the reactor's mechanical and thermal robustness during system fault conditions.
- Loss Measurement:Determines the reactor's efficiency (lower losses mean lower operating costs).
- Sound Level Test:Important for installations near populated areas or noise-sensitive environments.
A manufacturer's commitment to rigorous testing and quality control is a strong indicator of product reliability.
Evaluating Supplier Capabilities: Beyond the Product Specifications
Selecting the right shunt reactor involves more than just matching technical specs. Choosing a competent and reliable Reactor Manufacturer or Shunt reactor supplier is equally vital for project success.
6.1. Customization and Flexibility (OEM/ODM)
- Tailored Solutions:Can the supplier accommodate specific requirements beyond standard offerings? This includes non-standard voltage/current ratings, specific dimensions for retrofitting, unique terminal configurations, or special environmental considerations.
- OEM/ODM Services:Suppliers offering Original Equipment Manufacturer (OEM) or Original Design Manufacturer (ODM) services demonstrate flexibility and engineering depth to meet unique project needs.
6.2. Lead Time and Delivery Reliability
- Project Schedules:Manufacturing lead times for high-voltage equipment can be significant. Confirm the supplier's standard production times and their track record for on-time delivery, especially for projects with tight deadlines.
- Emergency Response:Assess their capacity to expedite orders for urgent requirements, if applicable.
6.3. Technical Support and After-Sales Service
- Pre-Sales Consultation:Does the supplier offer expert technical advice during the selection process?
- Installation and Commissioning Support:Availability of field service engineers or comprehensive documentation.
- Warranty and Long-Term Support:Clear warranty terms and availability of spare parts or repair services.
6.4. Experience and Reputation
- Track Record:Consider the supplier's experience, especially with similar projects or international installations. Case studies and references can be valuable.
- Global Reach:For international projects, a supplier with export experience understands logistical complexities and diverse standards.
Selecting the right shunt reactor requires careful analysis of application needs, electrical requirements, functional goals, construction preferences, quality standards, and supplier capabilities. A systematic approach ensures the reactor enhances power system stability, reliability, and efficiency.Partnering with an experienced Reactor Manufacturer can simplify this process. Companies like ZHIYOU (Shanghai Zhiyou Electric Power Equipment Co., Ltd.) offer a wide range of dry-type and oil-immersed shunt reactors across voltage and power ratings (e.g., 10kV-66kV, 1000A-8000A). Their ability to support diverse applications—from substations to renewable energy projects—and adherence to international standards (IEC, ANSI, GB), along with flexible OEM/ODM options and technical consultation, make them a reliable Shunt Reactor Supplier for high-voltage projects worldwide. A well-chosen shunt reactor, backed by a trusted partner, is key to a strong and efficient power grid.