In today’s world, where sustainability is no longer a buzzword but a business imperative, even seemingly mundane components like custom heat sinks are coming under intense environmental scrutiny. These unsung heroes of thermal management, crucial for keeping our electronics running cool and efficiently, are now being evaluated not just for their performance, but for their environmental footprint. From the materials they're made of to the processes used to manufacture them, every stage of a custom heat sink’s lifecycle is being examined for its impact on the planet. This article delves into the critical aspects of environmentally friendly custom heat sink materials, exploring the challenges, opportunities, and innovative solutions shaping the future of thermal management. Understanding these nuances is essential for businesses aiming to meet increasingly stringent regulations, satisfy environmentally conscious customers, and build a truly sustainable supply chain.
Table of contents:
Material Composition and Compliance: Avoiding the Toxic Trap
Sustainable Sourcing: Tracing the Origins of Heat Sink Materials
Pollution Control in Manufacturing: Minimizing the Environmental Footprint of Production
Recyclability and Degradability: Closing the Loop on Heat Sink Materials
Balancing Performance and Sustainability: Overcoming the Challenges
Extruded Profiles Heatsink
Tailoring Solutions to Specific Industries
Material Composition and Compliance: Avoiding the Toxic Trap
At the heart of any discussion about environmental responsibility lies the composition of the materials themselves. For heat sinks, this means a deep dive into what they're made of and whether those components pose a threat to human health or the environment.
The Core Elements: The primary concern revolves around the presence of internationally banned or restricted hazardous substances. Lead (Pb), cadmium (Cd), mercury (Hg), and hexavalent chromium (Cr(VI)) are notorious examples. These heavy metals, once common in various manufacturing processes, are now heavily regulated due to their toxicity and persistence in the environment.
Navigating the Regulatory Maze: Compliance with regulations like RoHS (Restriction of Hazardous Substances), REACH (Registration, Evaluation, Authorization and Restriction of Chemicals), and the growing demand for halogen-free materials is non-negotiable. RoHS, for instance, restricts the use of specific hazardous materials in electrical and electronic equipment sold in the European Union. REACH requires companies to register chemical substances and assess their potential risks. Halogen-free standards aim to eliminate or minimize the use of chlorine and bromine, which can release toxic dioxins and furans when incinerated.
The User's Perspective: The specific concerns vary depending on the industry.
Electronics and Medical Device Manufacturers: These sectors are particularly sensitive to heavy metal contamination. The presence of these substances can compromise the safety and reliability of their products, potentially leading to malfunctions or health hazards. Moreover, non-compliance can result in significant penalties and barriers to market access, especially in regions with strict environmental regulations like the EU.
Electric Vehicle (EV) Producers: The potential impact of toxic materials on battery system longevity is a major worry. Heavy metals can accelerate corrosion and degradation within battery components, shortening their lifespan and potentially leading to safety issues.
Industry in Action:
Apple's Rigorous Testing: Apple, known for its commitment to environmental responsibility, requires its heat sink suppliers to provide ICP-MS (Inductively Coupled Plasma Mass Spectrometry) test reports. This sophisticated analytical technique accurately measures the concentration of heavy metals in materials, ensuring compliance with Apple's stringent standards.
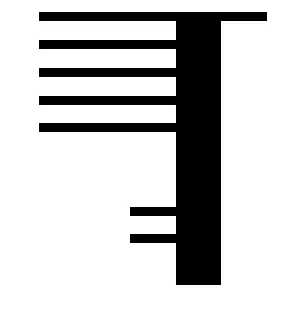
Sustainable Sourcing: Tracing the Origins of Heat Sink Materials
The journey of a heat sink material begins long before it enters a factory. Where those raw materials come from and how they're extracted are critical considerations for environmental sustainability.
The Power of Recycled Materials: A key strategy is to maximize the use of recycled materials, such as recycled aluminum and copper. Reusing these metals significantly reduces the energy required for primary production, lowers greenhouse gas emissions, and minimizes the need for resource extraction.
Addressing Conflict Minerals: The sourcing of certain minerals, particularly those from conflict-affected areas, poses significant ethical and environmental challenges. Conflict minerals, such as tin, tantalum, tungsten, and gold (often used in electronic components), can fuel armed conflicts and human rights abuses.
The User's Perspective:
Consumer Electronics Brands (Dell, HP): These companies are under increasing pressure to disclose the origin of their raw materials. This transparency is essential for meeting ESG (Environmental, Social, and Governance) reporting requirements and demonstrating a commitment to responsible sourcing.
Industrial Clients: These customers are focused on supply chain transparency to mitigate environmental compliance risks. They need assurance that their suppliers are adhering to ethical and sustainable practices.
Industry in Action:
Tesla's Aluminum Standard: Tesla requires its heat sink suppliers to use ASI-certified aluminum. The Aluminium Stewardship Initiative (ASI) promotes responsible production, sourcing, and stewardship of aluminum. ASI certification ensures that aluminum mining and production meet stringent environmental and social standards.
Pollution Control in Manufacturing: Minimizing the Environmental Footprint of Production
The manufacturing process itself can be a significant source of pollution. From the generation of harmful waste gases and liquids to the use of environmentally damaging chemicals, it's crucial to implement cleaner production methods.
Controlling Waste Streams: The production of heat sinks can generate hazardous waste streams, including acidic etching solutions and electroplating wastewater. Proper treatment and disposal of these wastes are essential to prevent soil and water contamination.
Adopting Cleaner Processes: Replacing traditional, polluting processes with more environmentally friendly alternatives is a key strategy. Examples include:
Cyanide-free electroplating: Cyanide is a highly toxic chemical used in some electroplating processes. Switching to cyanide-free alternatives significantly reduces the risk of environmental damage and worker exposure.
Water-based Cleaning Agents: Replacing organic solvents with water-based cleaning agents reduces volatile organic compound (VOC) emissions, which contribute to air pollution and smog formation.
The User's Perspective:
High-End Server Manufacturers (e.g., Inspur, Sugon): These companies typically require their suppliers to be certified under ISO 14001, an internationally recognized standard for environmental management systems. ISO 14001 certification demonstrates a commitment to continuously improving environmental performance.
Medical Device Companies: These customers often have stringent requirements for production cleanliness to avoid contamination. This includes minimizing dust particles and other potential contaminants that could affect the performance or safety of medical devices.
Industry in Action:
Intel's Wastewater Standards: Intel requires its heat sink suppliers to meet stringent wastewater discharge standards, such as those outlined in the Electronic Industry Pollutant Discharge Standard (GB 39731-2020) in China. These standards limit the concentration of pollutants that can be released into the environment.
Recyclability and Degradability: Closing the Loop on Heat Sink Materials
The end-of-life management of heat sinks is an increasingly important consideration. Designing heat sinks for easy recycling and exploring the use of biodegradable materials can significantly reduce their environmental impact.
Design for Disassembly: Designing heat sinks from easily separable materials, such as pure aluminum rather than aluminum-plastic composites, facilitates efficient recycling. This allows for the recovery of valuable materials and reduces the amount of waste sent to landfills.
Exploring Bio-Based Materials: Using bio-based materials, such as biodegradable thermally conductive plastics, can offer a more sustainable alternative to traditional metals. These materials break down naturally in the environment, reducing the long-term burden of waste.
The User's Perspective:
European Customers: Companies operating in Europe must comply with the Waste Electrical and Electronic Equipment (WEEE) Directive. This directive requires manufacturers to take responsibility for the end-of-life management of their products, including ensuring that heat sinks can be efficiently recycled.
Green Energy Companies: These organizations are increasingly interested in purchasing products made from biodegradable materials to minimize their environmental footprint.
Industry in Action:
Dell's Bamboo Fiber Heat Sinks: Dell has incorporated bamboo fiber composite materials into some of its laptop heat sinks. Bamboo is a rapidly renewable resource, and the composite material is partially biodegradable, reducing the reliance on non-renewable materials.
Balancing Performance and Sustainability: Overcoming the Challenges
The pursuit of environmentally friendly heat sink materials presents a key challenge: ensuring that these materials maintain the required thermal performance, mechanical strength, and corrosion resistance.
Addressing Performance Trade-offs: Environmentally friendly materials may sometimes have lower thermal conductivity or mechanical strength compared to traditional materials. It's crucial to identify and address these trade-offs through innovative design and material selection.
Leveraging Innovative Technologies: Advanced technologies can help bridge the performance gap. Examples include:
Nano-coatings: Applying nano-coatings to heat sink surfaces can enhance their thermal conductivity and corrosion resistance without compromising environmental friendliness.
Advanced Alloys: Developing new aluminum alloys with improved thermal properties and reduced environmental impact can provide a sustainable alternative to traditional alloys.
The User's Perspective:
Data Center Operators: Data centers rely on efficient cooling systems to prevent servers from overheating and failing. They cannot afford to compromise on thermal performance in the name of environmental sustainability.
Automotive Industry: The automotive industry is striving to reduce vehicle weight to improve fuel efficiency and reduce emissions. However, they must also ensure that cooling systems remain robust and reliable.
Industry in Action:
Panasonic's Graphene-Enhanced Aluminum Alloys: Panasonic has incorporated graphene-enhanced aluminum alloys into heat sinks for 5G base stations. Graphene's exceptional thermal conductivity boosts the overall performance of the heat sink while reducing the amount of material required.
Extruded Profiles Heatsink
Advantage: Extruded Profiles Heatsink is a type of heat sink produced by the extrusion process. In this process, aluminum or other metals are shaped by forcing them through a die to create the desired cross-sectional profile. Extruded heat sinks are known for their versatility, cost-effectiveness, and ability to be customized to various shapes and sizes.
Environmental Benefits:
Material Efficiency: Extrusion allows for the efficient use of materials, minimizing waste during the manufacturing process. The ability to create complex shapes with precise dimensions reduces the need for secondary machining operations, which can generate additional waste.
Recyclability: Aluminum, a common material for extruded heat sinks, is highly recyclable. This means that end-of-life heat sinks can be recycled and reused, reducing the demand for new materials and lowering the environmental impact.
Customization: Extrusion enables the creation of custom heat sinks tailored to specific applications. This level of customization ensures that the heat sink provides optimal cooling performance, reducing the overall energy consumption of the electronic device it serves.
Tailoring Solutions to Specific Industries
The specific environmental concerns and requirements vary significantly across different industries. To effectively address these needs, heat sink manufacturers must tailor their solutions to meet the unique demands of each sector.
Consumer Electronics: Focus on RoHS compliance, halogen-free materials, and lightweight designs to reduce the carbon footprint of devices. Meet standards like Apple's Regulated Substances List.
Industrial Equipment: Emphasize material durability, corrosion resistance, and recyclability. Provide long-term guarantees of corrosion resistance.
Electric Vehicles: Prioritize conflict mineral avoidance, material traceability, and compliance with regulations like the EU Battery Directive.
Aerospace: Focus on high-performance, environmentally friendly alternative materials and meet standards like AS9100D.
The shift towards environmentally responsible heat sink materials is not merely a trend; it's a fundamental transformation driven by regulatory pressures, consumer demand, and a growing awareness of the importance of sustainability. By prioritizing material composition, sustainable sourcing, pollution control, recyclability, and performance, businesses can create a new generation of heat sinks that are both effective and environmentally friendly. Embracing these principles is not only good for the planet, but it also makes good business sense, enhancing brand reputation, reducing risks, and opening up new market opportunities.As companies navigate this evolving landscape, choosing partners committed to both innovation and environmental stewardship becomes crucial. With a focus on sustainable practices and cutting-edge thermal management solutions, companies like Renxin are well-positioned to help businesses achieve their environmental and performance goals.
No comments:
Post a Comment