In the modern manufacturing landscape, sustainability is no longer optional — it is a requirement. As industries grow increasingly focused on reducing their carbon footprint, energy efficiency has become a top priority for manufacturers globally. One area that has gained significant attention is the energy consumption of laser pipe cutting machines. These machines, widely used in sectors like metalworking, automotive, renewable energy, and even flask and bottle manufacturing, are essential for precise cutting of pipes and tubes. However, they are also known to consume substantial amounts of energy during operation.The growing demand for energy-efficient manufacturing practices presents both a challenge and an opportunity for businesses. Manufacturers are not only looking to reduce costs and increase productivity but are also striving to meet the expectations of environmentally conscious consumers. In this article, we’ll explore various ways to maximize the energy efficiency of laser pipe cutting machines, providing practical insights for manufacturers to implement energy-saving strategies while maintaining top performance.
Table of contents:
Energy Consumption and Power Requirements
Automation and Energy-Saving Control Systems
Long-Term Operational Energy Management
Integration with Other Equipment for Enhanced Efficiency
Energy Consumption and Power Requirements
One of the most critical factors in determining the overall energy efficiency of laser pipe cutting machines is their power consumption. These machines consume varying amounts of power depending on several factors, including the type of laser used, the complexity of the cutting process, and the operational mode of the machine.
Laser Types: The type of laser used in the cutting machine plays a significant role in its energy consumption. Fiber lasers, for example, are much more energy-efficient than CO2 lasers. Fiber lasers convert more of the electrical input into laser output, reducing the amount of energy wasted as heat. This can lead to up to 30% greater energy efficiency compared to traditional CO2 lasers. As fiber lasers become more prevalent in the market, manufacturers, like JACKSON, are increasingly adopting them as their laser source of choice.
Energy Usage During Different Stages: Laser cutting machines typically go through several stages during operation, from startup to cutting to standby. The energy consumed during idle or standby phases is much lower than during active cutting. Smart energy management systems, which adjust the power based on real-time needs, can significantly reduce energy consumption by optimizing power usage during these non-cutting phases.
Optimizing Power Output: Another way to improve energy efficiency is by ensuring that the machine operates within its optimal power range. This involves selecting a laser cutting machine that has the appropriate power output for the material being cut. Overusing power can lead to unnecessary energy consumption and increased wear on the machine. Additionally, power optimizations, such as laser beam intensity adjustments, can help achieve a balance between performance and energy use.
Energy Recovery and Reuse
As manufacturers become more committed to sustainability, energy recovery and reuse systems are gaining importance. These systems help reduce the overall energy demand by capturing excess energy from various processes and using it in other parts of the operation.
Heat Recovery Systems: Laser cutting machines generate a significant amount of heat, which can be wasted if not managed properly. Some advanced systems are equipped with heat recovery technology, which recycles this waste heat for use in other areas of the facility. For example, the recovered heat can be redirected to pre-heat the materials before they are cut or used to support other energy-intensive systems, like the air conditioning or heating systems in the factory.
Energy Regeneration: Some high-end laser cutting machines feature energy regeneration systems, which capture and store excess energy produced during certain processes. This energy can then be reused later in the operation, reducing the need for external energy input. This not only saves on energy costs but also minimizes environmental impact by lowering overall energy demand.
Waste Heat Utilization: Waste heat can be channeled into systems like water heating or space heating, making use of energy that would otherwise go to waste. This integration of waste heat reuse further optimizes the overall energy efficiency of the entire manufacturing process.
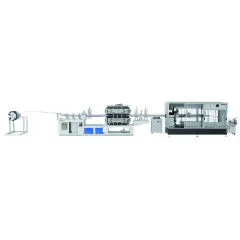
Laser Source Efficiency
The laser source is the heart of any laser cutting machine, and its efficiency is one of the most crucial factors influencing energy use. In recent years, the development of more efficient laser sources has played a pivotal role in improving the overall energy efficiency of laser cutting machines.
Fiber Lasers vs CO2 Lasers: As mentioned earlier, fiber lasers are much more efficient than traditional CO2 lasers. While CO2 lasers typically have a conversion efficiency of around 10%, fiber lasers achieve conversion efficiencies of up to 30%. This means that fiber lasers use far less energy to generate the same amount of cutting power, resulting in lower energy consumption and a more sustainable operation.
Beam Quality and Efficiency: The quality of the laser beam directly affects the cutting efficiency and the amount of power needed to achieve precise cuts. High-quality lasers ensure that less energy is wasted in the cutting process, reducing the overall power consumption. Additionally, high beam quality can also improve the cutting speed and accuracy, further enhancing the machine’s performance and efficiency.
Laser Source Longevity: An efficient laser source tends to have a longer lifespan. This reduces the need for frequent replacements, which helps to minimize waste and lower the environmental impact of manufacturing new laser sources. Longer-lasting lasers also reduce the frequency of maintenance, which in turn lowers energy consumption associated with repairs and downtime.
Automation and Energy-Saving Control Systems
In the modern era, automation is a key player in energy optimization. Laser pipe cutting machines that come equipped with advanced control systems can significantly reduce energy usage by automating processes and ensuring the machine operates as efficiently as possible.
Smart Energy Management: Many newer laser cutting machines, such as those provided by JACKSON, are equipped with smart energy management systems that monitor the energy usage in real-time and automatically adjust power levels based on factors such as material thickness, cutting complexity, and operating speed. This ensures that energy is only used when necessary and at the optimal level, significantly reducing energy waste.
Automatic Shutdown and Standby Features: A critical aspect of energy management in laser cutting machines is their ability to shut off or enter standby mode when not in use. Automatic shut-off systems ensure that machines do not consume unnecessary power during long breaks or periods of inactivity, helping to conserve energy.
Path Optimization: Some advanced laser cutting machines use intelligent path optimization algorithms to plan the most efficient cutting paths. By reducing unnecessary movements and cutting time, these systems help lower overall energy consumption and increase productivity.
Long-Term Operational Energy Management
Energy efficiency doesn’t just rely on one-off adjustments or upgrades — it requires ongoing attention to long-term operational factors. Manufacturers looking to improve energy efficiency in the long run need to focus on maintenance, training, and optimization.
Preventive Maintenance: Regular maintenance is essential to keep laser cutting machines operating at peak efficiency. For example, cleaning and replacing lenses, checking cooling systems, and calibrating power settings ensure that the machine runs smoothly, using the least amount of energy. Proper maintenance also reduces the risk of breakdowns, which can lead to unnecessary energy consumption during repairs.
Energy Monitoring and Analysis: By implementing energy monitoring systems, manufacturers can track power usage over time and identify inefficiencies or areas for improvement. This data-driven approach enables operators to optimize the machine’s settings and adjust operations to further reduce energy consumption.
Software Upgrades: Software updates often include energy-saving features, such as improved cutting algorithms or more efficient power management. Keeping the laser cutting machine software up to date ensures that the machine benefits from the latest energy efficiency enhancements.
Integration with Other Equipment for Enhanced Efficiency
Laser pipe cutting machines do not work in isolation; they are typically part of a larger production system that includes other equipment, such as automated material handling systems or cooling systems. By optimizing the entire system, manufacturers can achieve greater energy efficiency.
Coordinated Power Management: When laser cutting machines are integrated with other systems, such as automated material handling systems, energy consumption can be synchronized across the entire production facility. This reduces the need for excess energy and ensures that the entire manufacturing process is as energy-efficient as possible.
Shared Cooling Systems: Many laser cutting machines require cooling systems to prevent overheating. By using shared cooling systems across multiple machines, manufacturers can lower the overall energy demand and reduce the cost of operating separate cooling units.
Certifications and Green Standards
Manufacturers looking to showcase their commitment to energy efficiency can seek certifications and standards that demonstrate their dedication to sustainable practices.
Energy Star and Other Certifications: Laser cutting machines that meet Energy Star or similar energy efficiency certifications ensure that they meet or exceed strict energy-saving standards. These certifications help boost a company’s reputation and demonstrate to customers that the products are made with sustainability in mind.
ISO 50001: Manufacturers can pursue ISO 50001 certification, which focuses on energy management systems. This certification helps ensure that the facility optimizes energy use across all machines, including laser pipe cutting machines, reducing waste and improving overall efficiency.
Environmental Impact Reports: Regular sustainability and energy reports can help manufacturers track their progress toward sustainability goals and highlight the energy-efficient features of their machines. These reports not only provide transparency but also help in marketing efforts to attract environmentally conscious clients.
Maximizing energy efficiency in laser pipe cutting machines is no longer optional but essential for manufacturers looking to stay competitive in today’s environmentally-conscious market. By focusing on energy consumption, energy recovery, laser source efficiency, automation, and long-term operational management, manufacturers can significantly reduce their environmental impact while maintaining high productivity and performance. Additionally, when integrated with other systems, such as vacuum flask production lines, laser cutting machines can further enhance overall energy efficiency across the entire production process. Investing in energy-efficient laser pipe cutting machines, such as those provided by JACKSON, helps businesses meet sustainability goals while staying at the forefront of industry innovation.
No comments:
Post a Comment