As the world becomes more environmentally conscious, the demand for eco-friendly products has surged across industries. For businesses in the tech and electronics sectors, one area where sustainability is increasingly important is in the cooling solutions that help ensure optimal performance and longevity of electronic devices. Heat sinks, which are vital components in the cooling process of electronics, are no exception to this trend. As consumers and businesses alike begin to demand more sustainable and environmentally responsible products, heat sink manufacturers are stepping up to meet these needs. This article will explore the key eco-friendly considerations that should guide heat sink design and production, highlighting how manufacturers are adopting new materials and processes to minimize their environmental footprint.
Table of contents
The Growing Importance of Eco-Friendly Heat Sinks
Selecting Non-Harmful Materials: A Critical Step for Sustainability
Complying with International Environmental Standards
The Role of Transparent and Sustainable Supply Chains
Optimizing the Manufacturing Process to Minimize Waste
Designing for Longevity and End-of-Life Recycling
The Role of Certifications in Building Consumer Trust
The Growing Importance of Eco-Friendly Heat Sinks
The cooling of electronic devices is crucial to maintaining efficiency and preventing overheating, which can lead to device failure. Heat sinks, typically made of metals like aluminum and copper, play a vital role in this process by dissipating heat away from sensitive components. However, as environmental concerns grow, heat sink manufacturers are recognizing the importance of not only optimizing thermal performance but also considering the ecological impact of their products.
Today’s market demands heat sinks that are not only efficient in managing heat but also sustainable in terms of material sourcing, production processes, and end-of-life disposal. Let’s dive into the key environmental aspects that consumers and businesses are now considering when selecting heat sinks.
Selecting Non-Harmful Materials: A Critical Step for Sustainability
When it comes to heat sink manufacturing, the selection of materials is one of the most critical factors that influence its environmental footprint. Traditional heat sinks are often made of metals such as aluminum, copper, or zinc, which are generally more sustainable compared to plastics and composites. However, these metals can still contain harmful elements, such as lead, mercury, or cadmium, which can be dangerous to both human health and the environment.
In response to growing environmental concerns, many heat sink manufacturers have begun to adopt materials that are RoHS (Restriction of Hazardous Substances) compliant. RoHS certification ensures that no harmful substances are used in the manufacturing of electronic products, making them safer for both users and the environment. By using lead-free solder and selecting metals with low environmental impact, manufacturers can significantly reduce the potential harm that a product might cause throughout its lifecycle.
Moreover, the choice of coatings is another factor where sustainability plays a role. Many traditional coatings involve the use of toxic solvents or chemicals, which can be harmful to both the environment and the people involved in the manufacturing process. Manufacturers are increasingly opting for water-based or eco-friendly coatings that are non-toxic and free of volatile organic compounds (VOCs), further reducing the environmental impact of heat sinks.
Complying with International Environmental Standards
In addition to using non-harmful materials, heat sink manufacturers are also focused on ensuring their products comply with international environmental regulations. Two key standards that influence heat sink design are RoHS and WEEE (Waste Electrical and Electronic Equipment).
RoHS Compliance: This directive limits the use of six hazardous materials, including lead, mercury, and cadmium, in the manufacturing of electronic and electrical equipment. As a heat sink manufacturer, ensuring RoHS compliance guarantees that your product meets the highest global standards for environmental safety and helps avoid the use of harmful substances in production.
WEEE Compliance: This standard focuses on the recycling and disposal of electronic products. For heat sink manufacturers, adhering to WEEE guidelines ensures that once the heat sink reaches the end of its life cycle, it can be safely dismantled and recycled, reducing waste and the environmental impact of discarded electronic components.
The Role of Transparent and Sustainable Supply Chains
In today’s market, consumers and businesses are becoming increasingly aware of the environmental impact of products at every stage of their lifecycle, from raw material extraction to manufacturing and eventual disposal. One of the key considerations for heat sink manufacturers is the sourcing of raw materials.
Ethical and sustainable sourcing of materials is crucial to ensuring that the environmental impact of heat sink production is minimized. For example, using recycled metals in the production of heat sinks can significantly reduce the need for mining and processing virgin materials, thus saving energy and reducing waste. Furthermore, heat sink manufacturers are becoming more transparent in their supply chains, providing consumers with clear information about where their materials come from and how they are sourced. This transparency helps build trust with customers who prioritize sustainability in their purchasing decisions.
By working with suppliers that prioritize eco-friendly practices, manufacturers can ensure that their products meet the highest standards of sustainability and help reduce the overall environmental footprint of the industry.
Optimizing the Manufacturing Process to Minimize Waste
Once the materials are sourced, the next step is to ensure that the manufacturing process itself is as environmentally friendly as possible. Traditional manufacturing processes for heat sinks can produce significant waste, whether in the form of metal shavings, scrap material, or excessive energy consumption.
To address these concerns, heat sink manufacturers are turning to advanced manufacturing technologies that reduce waste and energy use. For instance, techniques such as precision casting or additive manufacturing (3D printing) are being used to create more efficient designs with minimal waste. These techniques allow manufacturers to use only the exact amount of material needed, reducing the scrap generated during production.
Additionally, many manufacturers are optimizing their processes to reduce energy consumption. By employing energy-efficient machinery and using renewable energy sources, manufacturers can further reduce their carbon footprint and contribute to global efforts to combat climate change.
Designing for Longevity and End-of-Life Recycling
A product’s longevity plays a significant role in its overall environmental impact. Heat sinks that are durable and have a long lifespan help reduce the need for frequent replacements, which in turn lowers waste and resource consumption. Manufacturers are increasingly focusing on designing heat sinks that can withstand the test of time, reducing the environmental impact associated with the disposal of short-lived products.
Moreover, manufacturers are ensuring that heat sinks are designed with recycling in mind. By using materials that are easily recyclable and designing products that can be easily disassembled, manufacturers enable more efficient recycling processes at the end of the product’s life. This contributes to a circular economy where products and materials are continuously reused, minimizing waste and the consumption of new resources.
The Role of Certifications in Building Consumer Trust
As consumers become more environmentally conscious, certifications have become an essential part of the purchasing decision-making process. Heat sink manufacturers that offer products with recognized eco-certifications can build trust with their customers. Labels like the Green Label or Eco-Label indicate that a product has been tested and verified to meet specific environmental standards.
Additionally, ISO 14001 certification, which focuses on environmental management systems, demonstrates a manufacturer’s commitment to continuously improving their environmental performance. This certification assures customers that the heat sink manufacturer is taking active steps to minimize its environmental impact, from sourcing raw materials to production and disposal.
As the demand for sustainable and eco-friendly products continues to rise, heat sink manufacturers are embracing a wide range of strategies to reduce their environmental footprint. From using non-harmful materials and adhering to global environmental standards to optimizing manufacturing processes and designing for longevity, these companies are paving the way for a more sustainable future in electronics. By prioritizing sustainability in every step of the production process, heat sink manufacturers are not only helping to protect the planet but also gaining a competitive edge in a market that increasingly values eco-conscious products. At Renxin, they understand the importance of sustainability and are committed to providing high-quality heat sink solutions that meet both performance and environmental standards.
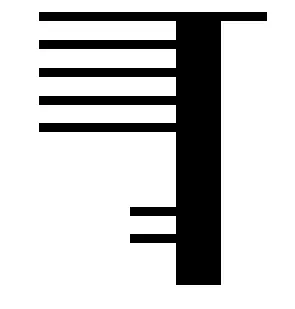
No comments:
Post a Comment